ORIGINAL PRODUCTS 自社装置
※画像をクリックすると詳細が見れます。
-
自動はんだ付け装置
-
自動はんだ付け装置
-
自動はんだ付け装置
-
スプレーフラクサ装置
-
スプレーフラクサ装置
-
自動はんだ付け装置
-
自動はんだ付け装置
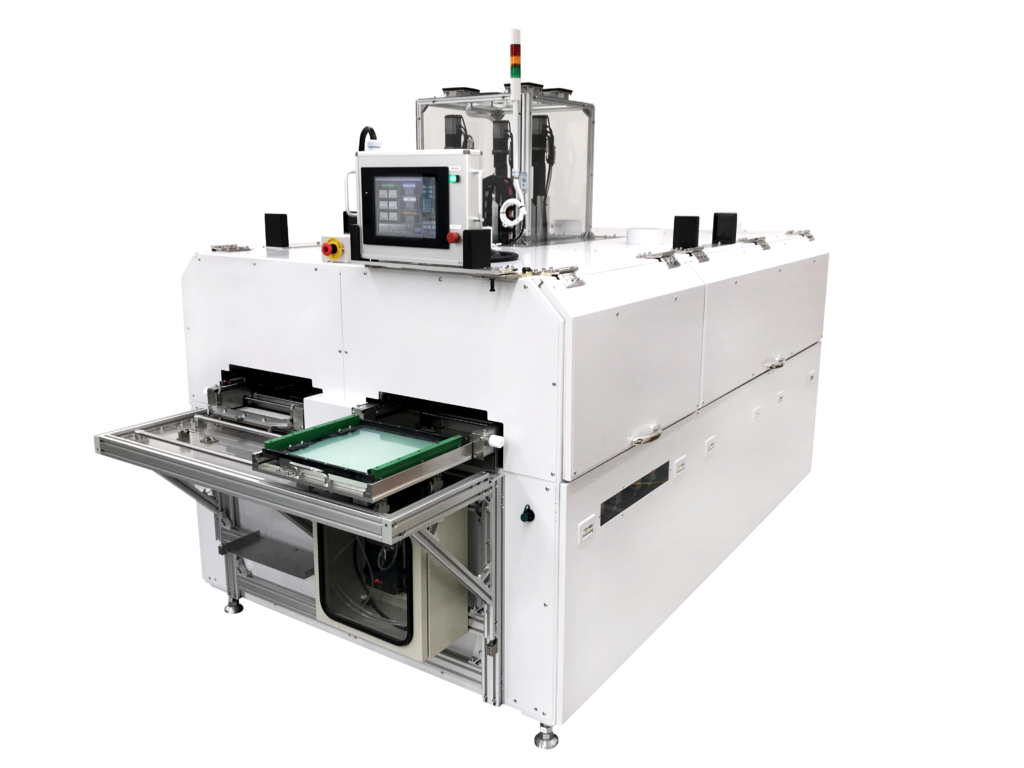
FXM-1
スマートディップⅡ
<高品質・高安定性実現>
<多彩な条件設定可能>
<無停止自動段取り替え>
装 置 仕 様
【適用ワークサイズ】
定型サイズパレット:350×380mm(パレット外形)
250×330(基板外形最大 ※部品押さえなどの形状により変動します)
部品高さ(パレット含む)制限:基板下=20mm/上=60mm
【スプレーフラクサ】 内蔵 XYプログラム式
低圧スプレー1基標準/集塵ブロワー/フラックス自動供給機構
【はんだ槽】 材質:ステンレス材+窒化処理
方式:撹拌式 加熱方式:間接加熱ヒータ
【はんだ容量】 約270Kgf(鉛フリーはんだ)
【はんだ液面キャリブレーション機構】 標準装備
【スキージ機構】 自動(ステッピングモータ駆動 デジタル設定)
【撹拌機構】 ステッピングモータ駆動(範囲・速度 デジタル設定)
【プリヒータ】 下面IRパネルヒータ 2kW 4ステージ独立温調
【搬送方式 】
入口→スプレー→プリヒータ&冷却:チェーンコンベア
ワーク移載機構(ロボシリンダー)
ディップ部自走ローラーコンベア(ステッピングモータ駆動)
【DIP方式】 浸責深さPG可変、ディップスライドモード
【ピールバック機構】
7パターン(3軸ロボシリンダー駆動)+引きずり動作
【冷却機構】 冷却排出コンベア(上下クロスフローファン)
【2Dコード読み取り自動段替え】 標準装備
【登録機種数】 標準 100機種
【電源 ・エアー】 3相200V 125A ・ 0.5MPa クリーンエアー
【装置重量】 約1900kgf
【外形寸法】 1590(W)×2580(D)×1400(H)mm
※入り出口パレットスライダー装着時 3125(D)mm
「FXM-1PR動画」はこちら↓
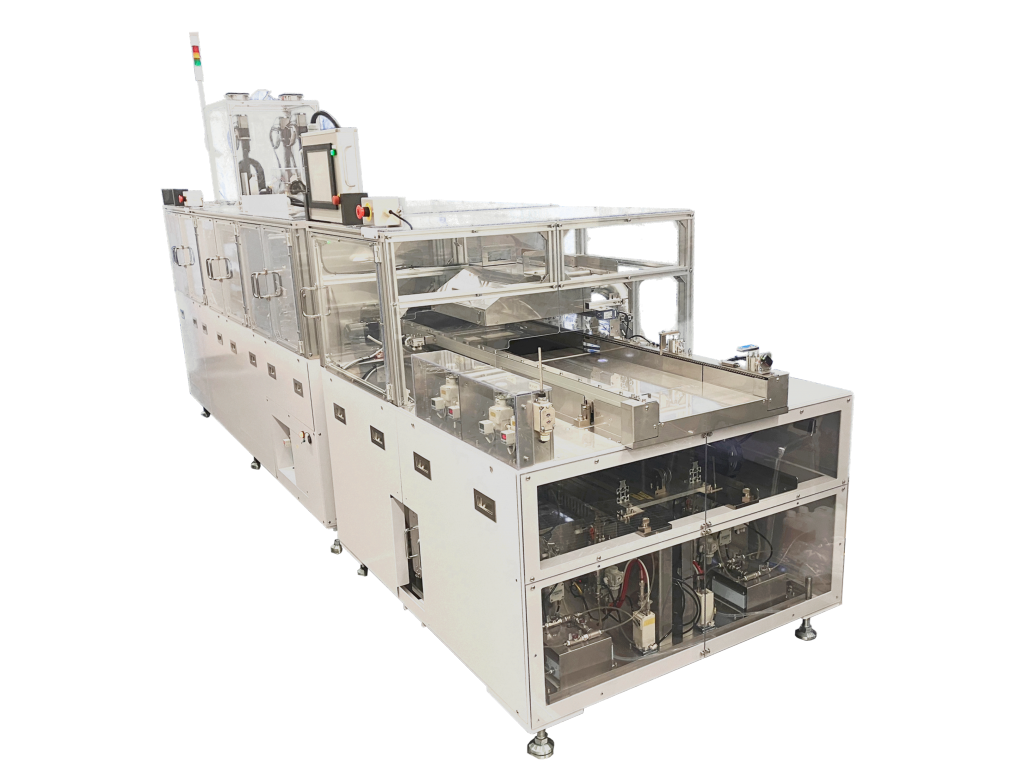
FXM-2
スマートディップⅡインライン
<高品質・高安定性実現>
<多彩な条件設定可能>
<無停止自動段取り替え>
装 置 仕 様
【適用ワークサイズ】
定型サイズパレット:350×380mm(パレット外形)
250×330(基板外形最大 ※部品押さえなどの形状により変動します)
部品高さ(パレット含む)制限:基板下=20mm/上=60mm
【スプレーフラクサ】 内蔵 XYプログラム式
低圧スプレー1基標準(オプションにて1基追加可能)/集塵ブロワー/フラックス自動供給機構
【はんだ槽】 材質:ステンレス材+窒化処理
方式:撹拌式 加熱方式:間接加熱ヒータ
【はんだ容量】 約270Kgf(鉛フリーはんだ)
【はんだ液面キャリブレーション機構】 標準装備
【スキージ機構】 自動(ステッピングモータ駆動 デジタル設定)
【撹拌機構】 ステッピングモータ駆動(範囲・速度 デジタル設定)
【プリヒータ】 下面IRパネルヒータ 2kW 4ステージ独立温調
【搬送方式 】
入口→スプレー→プリヒータ:チェーンコンベア
ディップ部自走ローラーコンベア(ステッピングモータ駆動)
【DIP方式】 浸責深さPG可変、ディップスライドモード
【ピールバック機構】
7パターン(3軸ロボシリンダー駆動)+引きずり動作
【2Dコード読み取り自動段替え】 標準装備
【登録機種数】 標準 100機種
【電源 ・エアー】 3相200V 125A ・ 0.5MPa クリーンエアー
【装置重量】 投入口からフラクサ部約200kgf・プリヒータから出口部約1300Kgf
【外形寸法】 連結時1200(W)×4997(D)×1400(H)mm
※FXM-1と基本性能は同等になります。
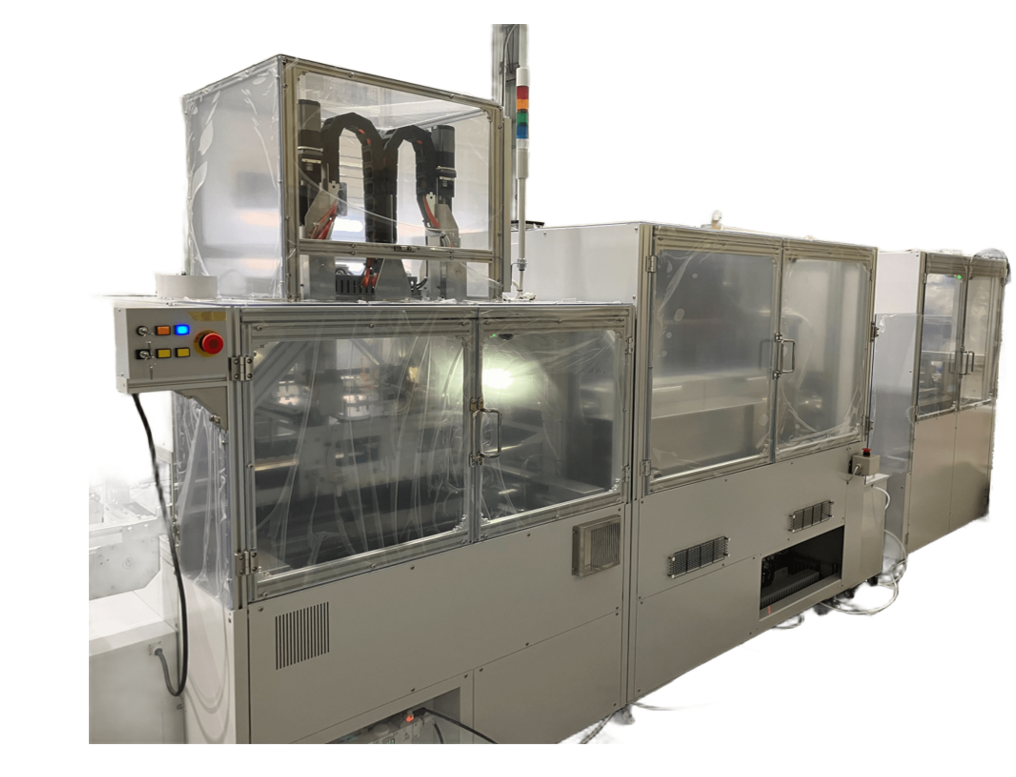
FXL-1
スマートディップL
<高品質・高安定性実現>
<多彩な条件設定可能>
<無停止自動段取り替え>
装 置 仕 様
【適用ワークサイズ】
定型サイズパレット:480×580mm(パレット外形)
380×510(基板外形最大 ※部品押さえなどの形状により変動します)
部品高さ(パレット含む)制限:基板下=25.4mm/上=150mm
【スプレーフラクサ】 内蔵 XYプログラム式
低圧スプレー1基標準/集塵ブロワー/フラックス自動供給機構
【はんだ槽】 材質:鋳物(FC300)
方式:撹拌式 加熱方式:間接加熱ヒータ
【はんだ容量】 約480Kgf(鉛フリーはんだ)
【はんだ液面キャリブレーション機構】 標準装備
【プリヒータ】 下面熱風循環式 / 2 ステージ独立温調 / 入出口シャッター機構
【搬送方式 】
入口 / フラクサ / プリヒータ:チェーンコンベア
かくはんディップユニット:ローラースライダー + 押し出し式
出口排出待機バッファ:コロコン式
【DIP方式】 浸責深さPG可変
【ピールバック機構】
7パターン(3軸ロボシリンダー駆動)
【2Dコード読み取り自動段替え】 標準装備
【登録機種数】 標準 999機種
【電源 ・エアー】 3相200V 145A ・ 0.5MPa クリーンエアー
【装置重量】 3,191kgf
かくはんディップユニット1,208kgf / プリヒータユニット1,135kgf / XY フラクサユニット648kgf / 制御200kgf
【外形寸法】 連結時6,068.7(W)× 2,815(D)×2,050(H)mm
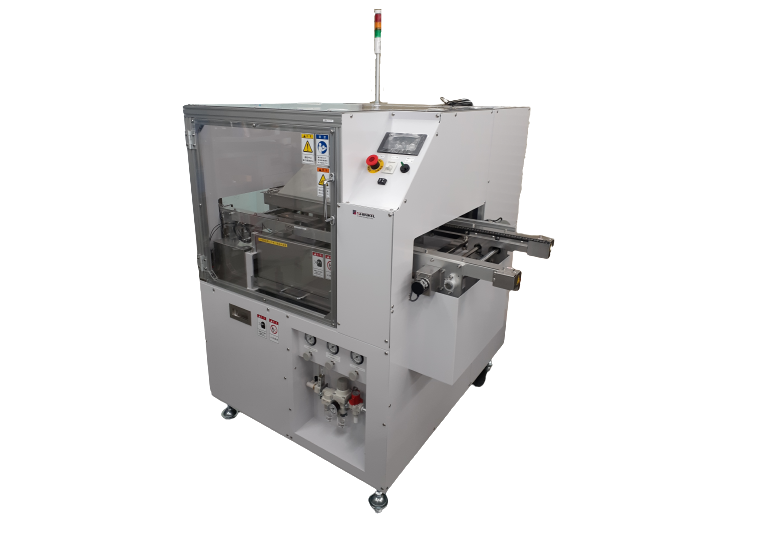
FMR-1/FML-1
多機能スイング式フラクサー装置
<多彩な塗布パターン>
<フラックス使用量削減で低環境負荷>
<取り扱い性・メンテナンス性向上>
装 置 仕 様
【適用ワークサイズ】● FAシンカテクノロジー 定型DIPパレットの場合
DIPパレットサイズ最大:300×380mm
基板最大サイズ 250×330(基板外形最大 ※部品押さえなどの形状により変動します)
部品高さ(パレット含む)制限:基板下=20mm/上=60mm
● 一般DIPパレットの場合
DIPパレットサイズ最大:300×380mm
基板最大サイズ 250×330(基板外形最大 ※部品押さえなどの形状により変動します)
部品高さ(パレット含む)制限:基板下=20mm/上=60mm
● 生基板搬送の場合
最大サイズ:300×380mm 基板厚み1㎜以上 搬送しろ3mm以上 (基板反り無きよう配慮ください。)
部品高さ制限:基板下=20mm/上=60mm
【コンベア幅・最大搬送速度】 幅可変(最大300㎜) ・ 2m/min
【登録機種数】 99機種
【外形寸法】 1200(W)×1320(D)×1350(H)mm (突起物除く)
「FMR-1PR動画」はこちら↓
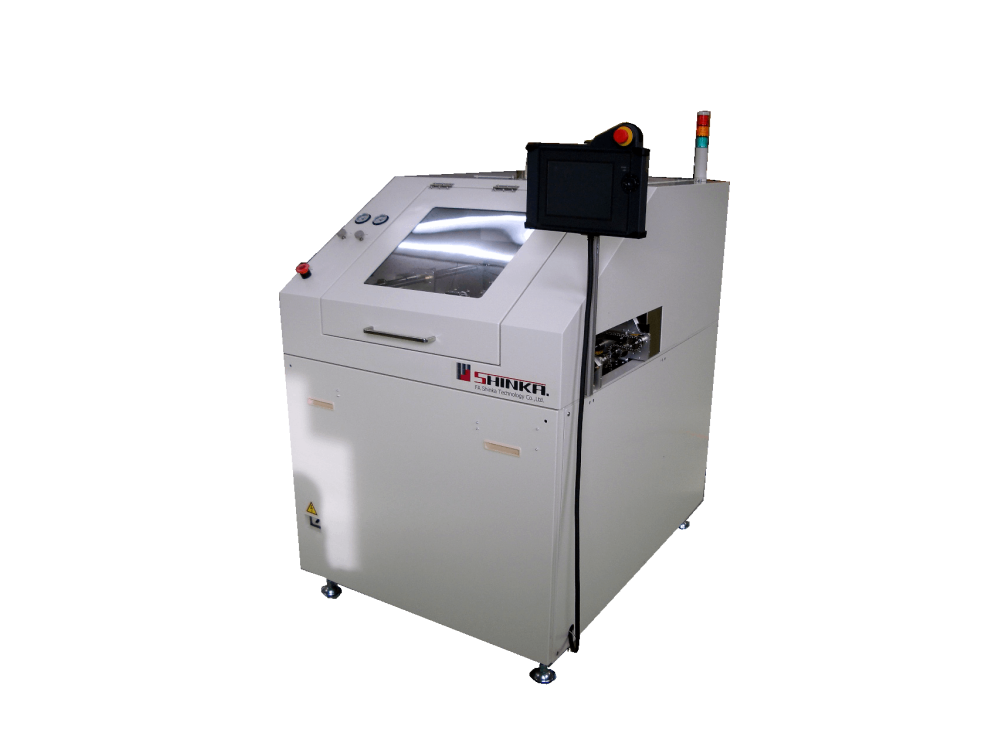
MFM-2533
インラインXYスプレーフラクサー装置
<必要部分に必要量を塗布>
<機種プログラムで条件変更>
<汚れにくく、清掃しやすい>
装 置 仕 様
【適用ワークサイズ】 250×330mm(基板またはパレット外形)
部品高さ制限:上=50mm/下=15mm
【スプレーノズル】 低圧2流体
【最小塗布幅】 15㎜
【塗布速度】 ポイント毎プログラム設定(1~100mm/sec)
【塗布ポイント】最大 100ポイント/プログラム
【登録機種数】 100機種
【フラックス容器】 自動供給
【プログラム方式】 目視ティーチング・座標入力
【電源・エアー】 単相200V ・ 0.5Mpa クリーン・ドライエアー
【外形寸法】 1,100(W)×1,200(D)×1,300(H)
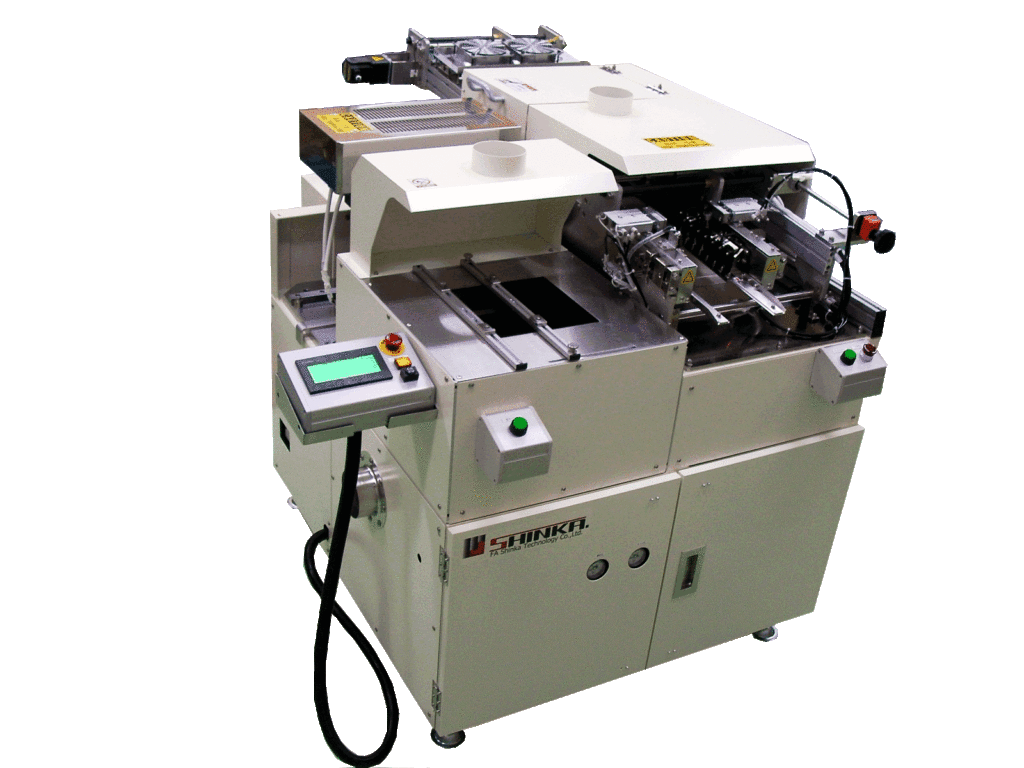
SSF-200-B3
超小型オールインワンはんだ付装置
<多目的用途に使用可能>
<業界最小サイズフロー槽>
<1個流しセル生産対応>
装 置 仕 様
【適用ワークサイズ 】50×50~210(W)×230(L)mm以内
厚さ:0.8~2.3t 部品高さ制限:基板上=50mm/基板下=6mm
【スプレーフラクサ 】低圧スプレーノズル×1
【スプレーノズル駆動 】XY 2軸ステッピングモータ駆動
MAX100mm/sec
【スプレーフラクサ】セットステージ ユニバーサルレール(手動可変)
【はんだ槽形式 】インバータ駆動噴流モータ×2 間接加熱ヒータ(1.2kW*6) カナックサーフ処理
【はんだ容量 】約170Kgf(鉛フリーはんだ)
【はんだ槽引き出し機構】手動ハンドル式
【噴流ノズル形式 】
1波:チップ対応ウェーブノズル 2波:整流ノズル
【予熱ヒータ 遠赤パネルヒータ】1kW
【はんだ付部搬送方式 】基板チャック往復移動
ステッピングモータ駆動
【幅可変方式】 ハンドル式(デジカウンター)
【搬送角度 】 5°
【出口リリース受け】 傾斜スライダー(フリーレイアウト)
【基板保持爪】 耐熱樹脂製
【冷却機構】 上部冷却ファン
【基板リリース機構】
セットステージ:エアシリンダー 出口部:カムブロック
【オペレーション】 タッチパネル(フリーレイアウト)
【登録条件数】 100機種
【電源 ・ エアー】 3相200V 10KVA・0.5MPaクリーンエアー
【外形寸法 】 960(W)×1355(D)×1190(H)mm
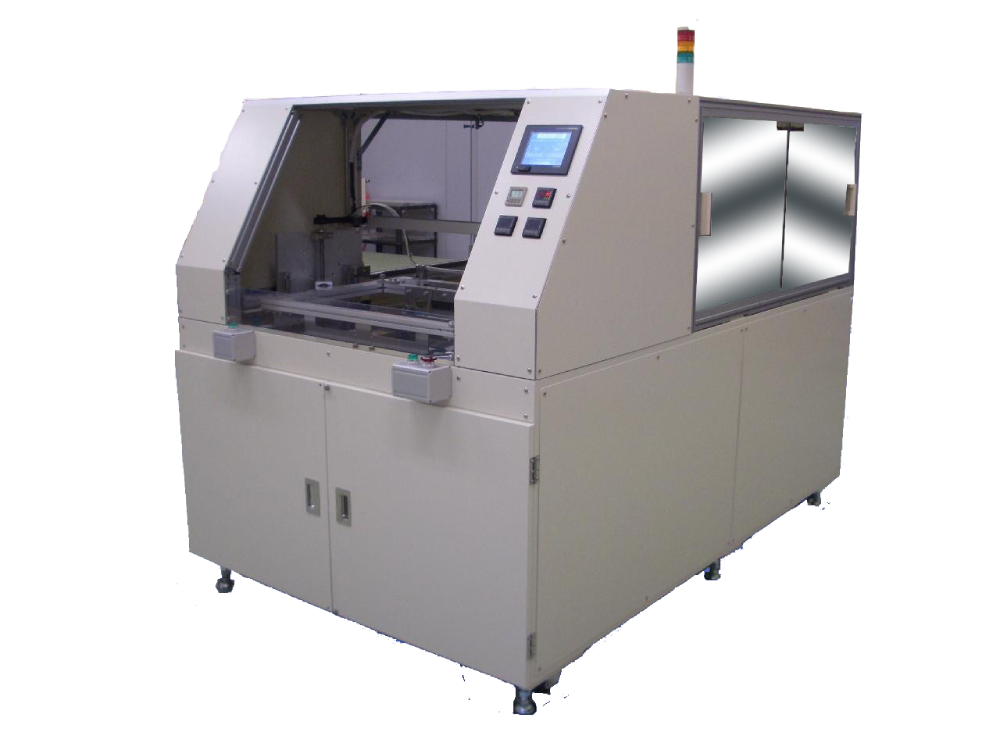
FZH-4639
スマートディップ リターンバックタイプ
<低流速はんだ付け>
<ロングリード対応可能>
<セル生産対応>
装 置 仕 様
【適用ワークサイズ】 460×390mm(パレット外形)以内
400×330(基板外形 参考サイズ)
部品高さ(パレット含む)制限:基板下=30mm
【スプレーフラクサ】 別置き ※オプション
【はんだ槽形式】 攪拌式(PAT.) 間接加熱ヒータ カナックサーフ処理
【はんだ容量】 約260Kgf(鉛フリーはんだ)
【はんだ液面キャリブレーション機構】 ※オプション
【スキージ機構】 ステージ連動(ステッピングモータ駆動)
【攪拌機構】 ステッピングモータ駆動(範囲、速度設定)
【プリヒータ IRパネルヒータ】 2kW×2枚 (1ステージ)
【搬送方式 ステージ往復移動】 (ステッピングモータ駆動)
【DIP方式】 浸漬深さPG可変
【ピールバック機構】 傾斜1軸(ステッピングモータ駆動)+引きずり動作
【冷却機構】 上下冷却ファン
【2Dコード読み取り自動段替え】 ※オプション
【登録機種数】 100機種
【電源 ・ エアー】 3相200V 50A ・ 0.5MPaクリーンエアー
【外形寸法】 1360(W)×2138(D)×1600(H)mm
OTHER PRODUCTS 取り扱い製品
※画像をクリックすると詳細が見れます。(五十音順・敬称略)
※相互リンク希望の方は、お問い合わせください。
ORIGINAL PATENT 特許技術
弊社では挿入部品を得意とした製品を開発・製造しています。
各装置メーカーが独自の工法を確立する中で
弊社の独自技術としてはんだ付けの工法に関する特許技術をいくつか取得しています。
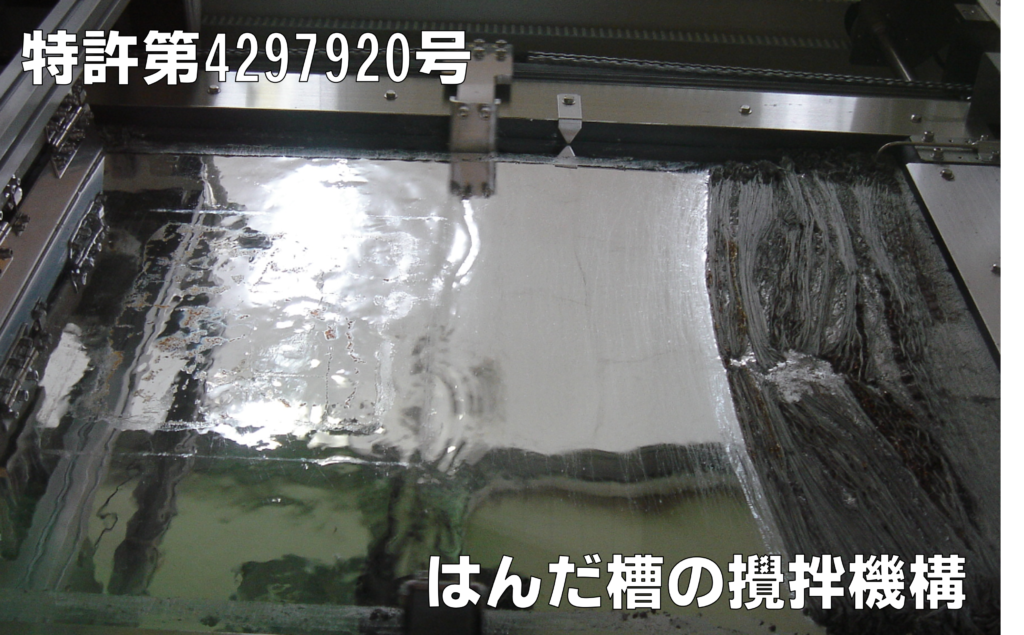
特徴
静止型はんだ槽の利点をそのまま継承する。
①噴流方式に比べて酸化物が非常に少ない。
②噴流方式のように、脈動による液面変動が少ない。
③噴流方式に比べて、槽内のはんだ容量が小さくできる。
静止型はんだ槽のデメリットを解消する。
・静止槽では、はんだの流れがないため、槽内の温度がばらつく。
⇒攪拌する事により温度のばらつきをなくす。
鉛フリーはんだ付けにおける接合信頼性が高い。
・噴流方式で必ず発生する、鉛フリーはんだによるCuパターン喰われが発生しない。
⇒はんだ付け時にパターン喰われが発生しないので、接合信頼性に優れている。
攪拌式+パレットによる部分ディップ
攪拌機構によりディップ直前にはんだ槽を撹拌し、温度ばらつきをなくした状態で基板をパレットごと浸漬ディップする。
・静止したはんだにより、均一な浸漬深さを得られることで、均一なはんだ付け品質が得られる。
・浸漬中にはんだを撹拌する事で熱交換を促進する事ができ、良好なはんだ付け品質が得られる。
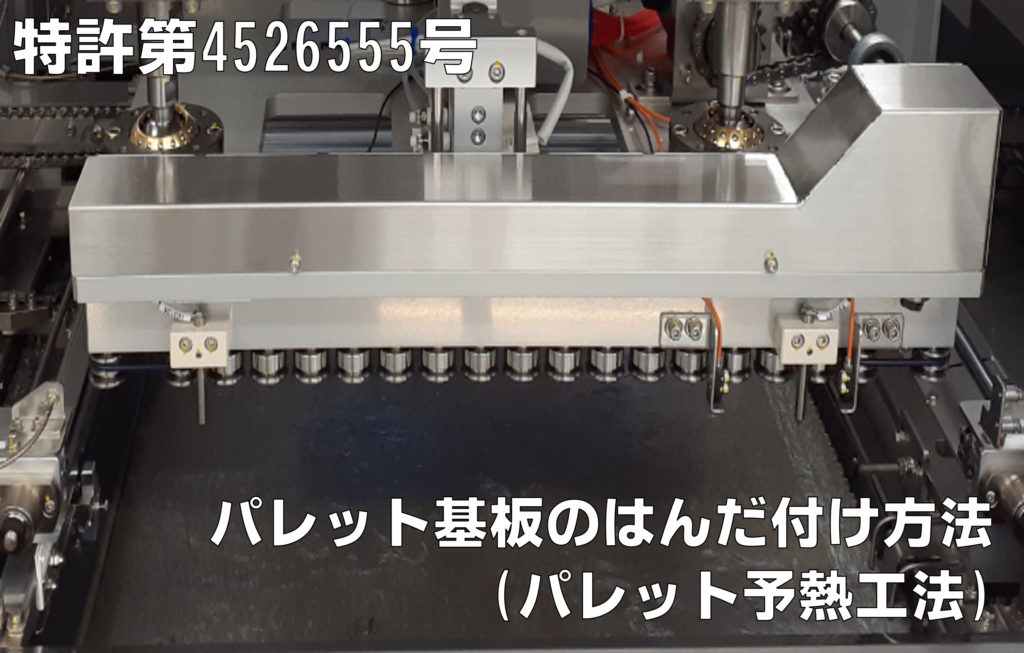
ディップパレットを使ったはんだ付けにおける、
予熱からはんだ付け時の熱効率を向上
目的
①予熱時間の短縮。
②はんだ付け時間内のディップパレットによる熱放散の軽減。
③予熱からはんだ付けのタイムラグ縮小
概要
パレットに基板が搭載された状態で、パレットだけをはんだ槽に浸漬させ加熱し、直後にはんだ付けを行う工法。
効果
はんだ槽の250~260℃均一な温度の液体に直接接触する為、熱伝達効率が良い⇒予熱時間を短縮できる。
部品には直接の熱が伝わらない為、熱に弱い部品へのダメージが少ない。
パレット予熱からディップへの移行が瞬間的に可能な為、予熱されたパレットの温度ドロップがないまま、はんだ付け工程に移行できる。
⇒はんだ付け中の熱回復時間を短縮し、良好なはんだ付け品質が得られる。
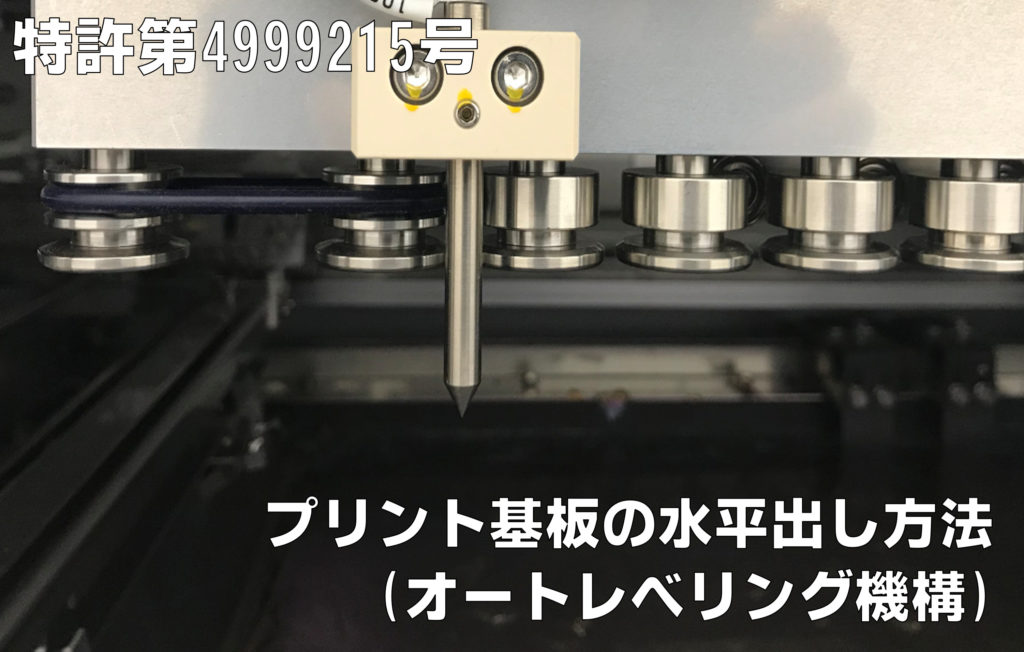
水平出し機構(オートレベリング)
はんだ付け時のワークの姿勢を、はんだ液面対して水平になるようにワークを保持している搬送機の姿勢を決める機構です。
はんだ液面は絶対水平ですが、搬送機は機械的に絶対水平を出す事は調整では不可能です。
本体のレベルが下記の図のように水平になっていなくても、はんだ付け時には水平になるように搬送機が動作します。
搬送機に①、②、③の接触センサーを設け、搬送機を降下させた時はんだ液面に同時に到達するように姿勢を制御します。
同時に接触した位置情報を水平とみなし制御する機構です。